
Careers
Are you ready to COME GROW WITH US?
We pride ourselves on our dedication to strive for continuous improvement, which cannot be achieved without the insight of our valued employees. It is our commitment to achieving these results and to retain employees by providing a positive and safe work environment. We reward performance and encourage loyalty, honesty and respect in our employees. It's about how well we work together and the image we project to the community, our clients, and our suppliers that sets us aside from the rest.
Ground Effects is an equal opportunity employer. We welcome and encourage applications from people with disabilities. Accommodations are available on request for candidates taking part in all aspects of the selection process.
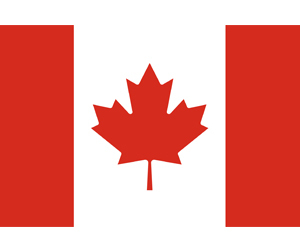
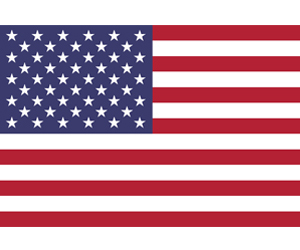